LSRP Services
- Preliminary Assessments/Phase 1 Property Audits
- Site Investigation - Testing to Determine if an Environmental Issue Exists
- Remedial Investigation – Delineation to Determine the Extent of the Environmental Issue
- Remedial Action Workplan – Provide a comprehensive scope of work required to remediate the Environmental Issue
- Remedial Action Report - Implementation of the Scope of Work to Remediate the Issue
- ISRA transactions
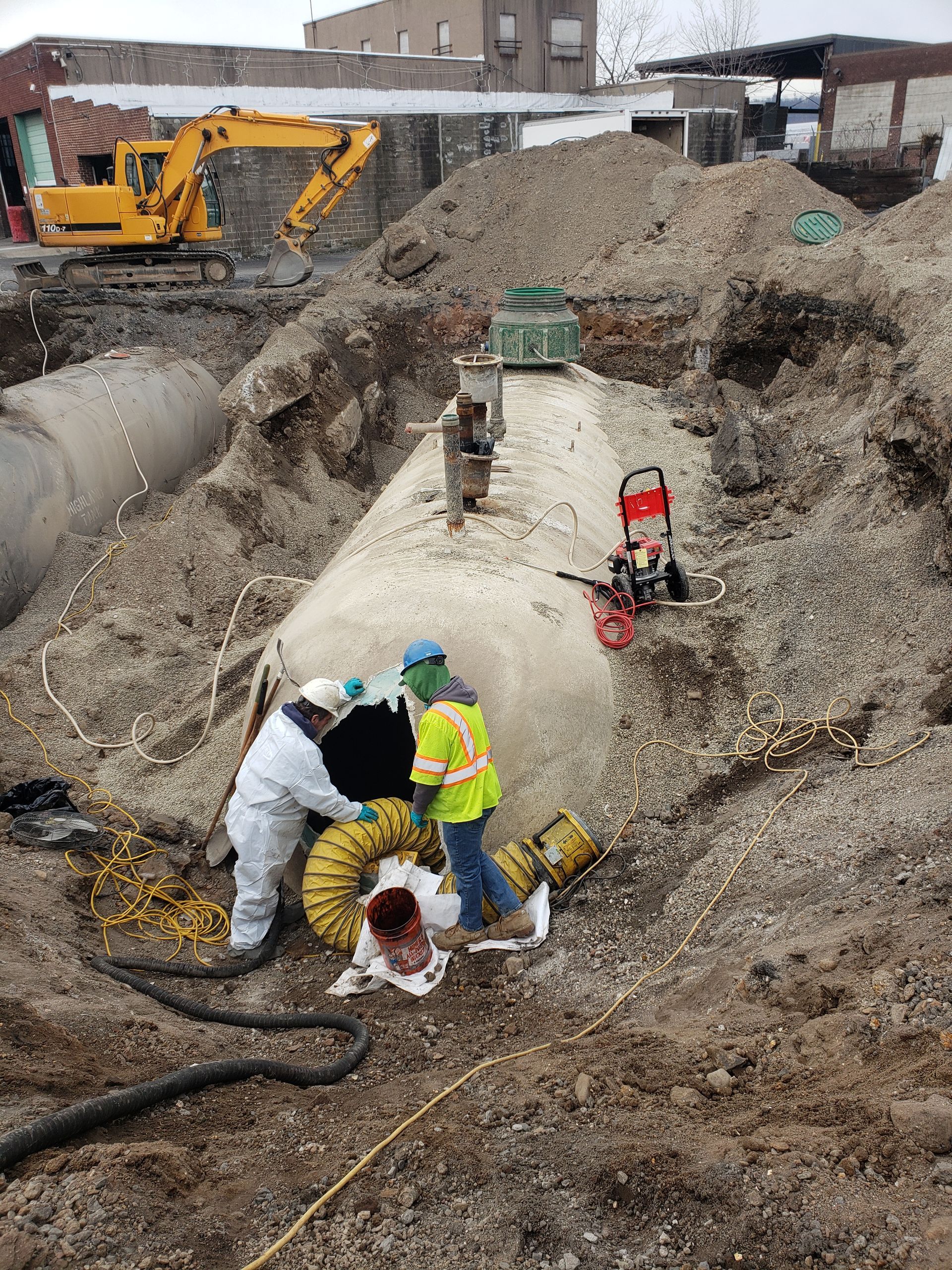
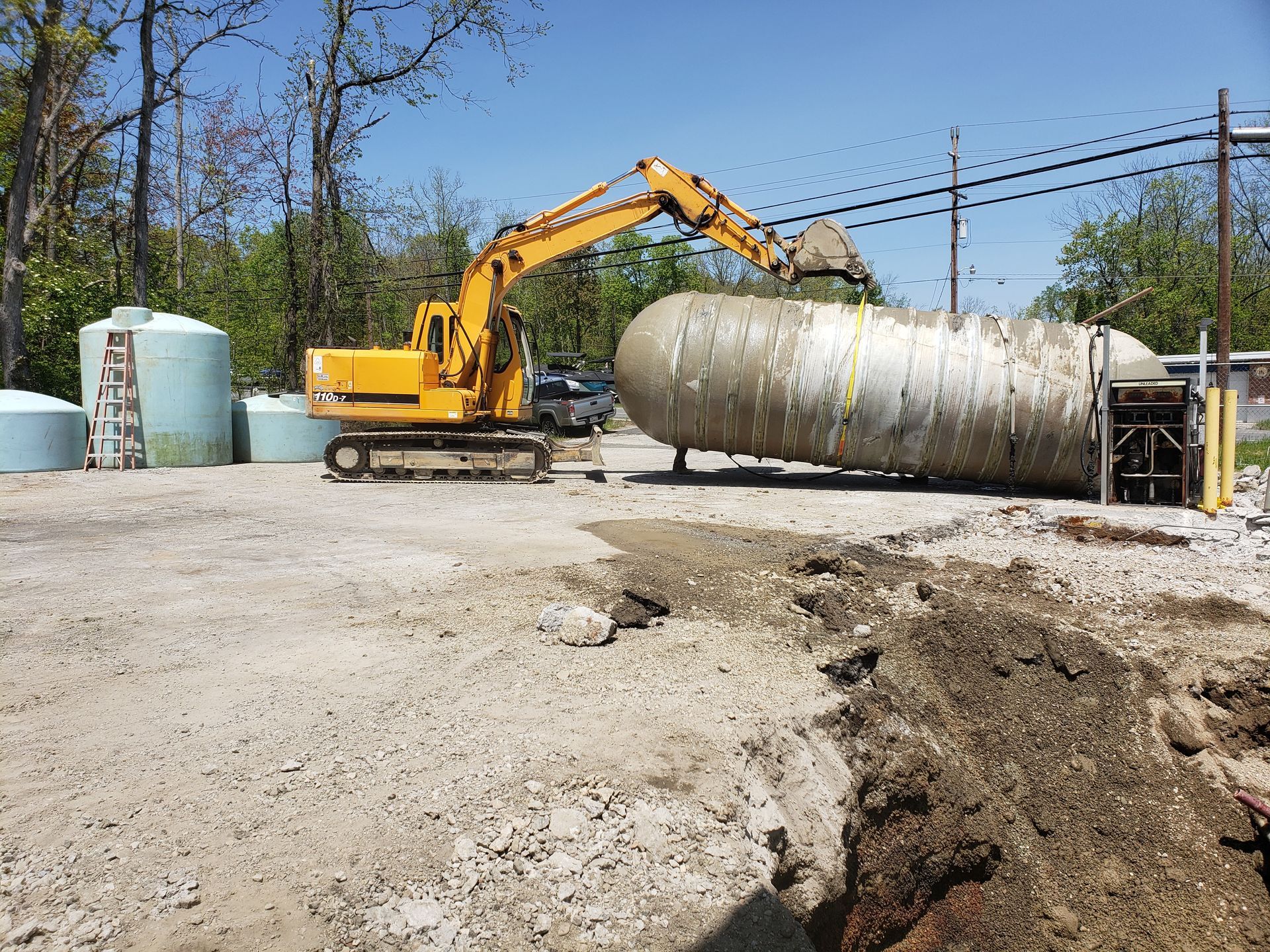
In 2009, the Site Remediation Reform Act set forth sweeping changes to the way in which sites are remediated in New Jersey. SRRA established the affirmative obligation for responsible parties to remediate contaminated sites in a timely manner. To achieve this goal, SRRA created a category of remediation professionals known as Licensed Site Remediation professionals (LSRP). LSRPs “step into the shoes” of the New Jersey Department of Environmental Protection (NJDEP) to oversee the remediation of contaminated sites. SRRA requires that the LSRP comply with all remediation statutes and rules and consider Department-developed guidance when making remediation decisions.
Under this new remediation paradigm, with very limited exceptions, the remediating party need not wait for the Department’s direction and pre-approvals to commence and continue cleanups. Instead, they must initiate and complete the cleanup under the direction of an LSRP, who has responsibility for oversight of the environmental investigation and remediation. The Department monitors the remediation progress and the actions of LSRPs by requiring the submittal of forms and reports as remediation milestones are reached.
Effective May 7, 2012 when the LSRP program was fully implemented, all remediating parties were required to retain an LSRP and remediate their site under the new LSRP paradigm, regardless of when the cleanup was initiated. Most often, the requirement to retain an LSRP is triggered when work on regulated underground storage tanks (USTs) is performed since all regulated USTs closures must be overseen by an LSRP. To obtain a Uniform Construction Code (UCC) permit for closure of regulated USTs, townships and cities will require issuance of a Closure – Notice of Intent (NOI) by an LSRP. Following issuance of the UCC permit, the LSRP will be required to provide the NJDEP with 14-day notice prior to initiating UST closure activities. Applied Service Corp. has 3 LSRPs on staff and we are ready to assist you with your regulated UST closure activities.
Our LSRPs can also assist you when you’re buying property in New Jersey. To qualify as an innocent purchaser under the New Jersey Spill Compensation and Control Act (Spill Act), you must perform the required due diligence of the property’s history. In NJ, that means performing a combined ASTM Phase I Environmental Site Assessment and Preliminary Assessment Report (Phase I/PAR) prior to purchasing the property. If the due diligence indicates that there are potentially contaminated areas of concern (AOCs), one is then required to perform a Site Investigation in those AOCs. Our LSRPs are qualified to perform the required due diligence investigations to help you to be considered as an innocent purchaser.
Our LSRPs can also assist you with complying with the Industrial Site Recovery Act (ISRA) which is triggered by selling property occupied by “industrial establishments” or when an industrial establishment ceases operations. The property owner or tenant are jointly and severally liable for complying with the provisions of ISRA which include submittal of an initial General Information Notice (GIN) and a Preliminary Assessment Report (PAR). The NJDEP requires that an LSRP be retained for all ISRA-subject transactions.
Soil Remediation
If a discharge of heating oil or any other hazardous material contaminates the soil to a degree that it exceeds the New Jersey Department of Environmental Protection (NJDEP) Soil Remediation Standards (SRS) the soil must be remediated or "cleaned up" to bring the site back into compliance with the applicable environmental standard.
For example, in some cases where there has been a discharge from an underground storage tank the soil may not be in violation of applicable NJDEP standard and we can just properly document the conditions and request that the NJDEP Case Manager close the case with a No Further Action (NFA) letter.
If not, the typical approach to remediating soil contamination is to remove the contaminated soil from the site and properly dispose of that material. This approach is the most time and cost effective in many cases. Applied Service Corp. has a fleet of excavating equipment and licensed waste-hauling vehicles to effectively perform a full range of projects on a turnkey basis, from the smallest homeowner oil tank leak to large-scale commercial and industrial remediation projects. We are a preferred contractor with many homeowner insurance carriers, insurance adjusters and environmental oversight consultants, especially on complex excavation projects requiring the removal of contaminated soil from beneath house structures. Our licensed Professional Engineering staff can evaluate and design the required structural supporting systems required for removal of impacted soils below load-bearing structures.
Groundwater Remediation
When groundwater is found to be contaminated above the applicable NJDEP Groundwater Quality Standards (GWQS), the groundwater must be remediated to bring the subject site back into compliance with those standards.
In cases where there is both soil and groundwater contamination, as in many residential oil tank cases, remediation of both media are usually performed at the same time. In those cases, we dewater the excavation via the use of one of our vacuum trucks, the installation of pumps or with a multi-point dewatering system. When a vacuum truck is utilized the wastewater is transported to a licensed recycling facility for disposal. When utilizing a pumping or dewatering system, the contaminated groundwater is treated on-site and discharged either back to the groundwater elsewhere on the site or to the local storm water drainage system, through an NJDEP-approved NJPDES permit.
In cases where the groundwater is contaminated , but the soil does not have to be remediated, we can remediate the ground water by several methods. In an effort to remediate a small plume of groundwater contamination, depending on the geology, one of the simplest methods is to install a monitoring well in the center of the plume and remove the contaminated groundwater and any floating product via Enhanced Fluid Recovery (EFR). This is performed with one of our vacuum trucks and can be quite effective in many cases. If EFR events do not prove to be effective, the full horizontal and vertical extent of the plume is determined through the installation of permitted ground water monitoring wells. Once the full extent of the ground water plume is determined, Applied Service Corp. will design and build the appropriate ground water treatment system with its staff of licensed Professional Engineers, Professional Geologists and professional trades personnel.
In-Situ Remediation
In-Situ remediation methods are commonly referred to as "Bio-Remediation", but bio-remediation is only one type of in-situ method. This common phrase comes from the earliest methods which introduced microbes that consumed certain pollutants. Today's methods are much more advanced and rely on several different means to get the job done.
These approaches vary project to project and are very site specific. The geology and existing environmental conditions play a very important role in determining the best in-situ approach to take. These methods are meant to change the environmental setting to enhance the natural biodegradation of the soil or groundwater or to cause a reaction that actually consumes the contaminant leaving behind harmless by-products. This is accomplished by introducing certain ingredients to the contaminated media, be it soil or groundwater to induce the necessary “reaction.”
In regards to remediating home heating oil, for example, there are means of enhancing the biodegradation potential of the soil or groundwater to help nature degrade the oil or by actually creating a chemical reaction that will consume the petroleum.
This technology is constantly evolving to remediate a greater number of contaminants in greater concentrations in differing environmental and geological settings. We perform and have access to all the latest proven technologies. Our staff of licensed professional engineers, professional geologists and professional trades personnel has the capability to design and build the appropriate in-situ treatment system to accelerate the degradation of contaminants at your site.